Thread lockers and bearing lockers
We stock a huge range of thread lockers and bearing lockers and also are a major importer of the Hernon Nuts N’ Bolts range. Each product has its own use and we’ll break that down here for you now. CTA Industrial threadlockers These are our own high-performance thread-locking fluids that are applied to Continue reading
Metal bonding glue
If you’re looking for a metal bonding glue, then we have lots to choose from. In short, it really depends on the application and what you are trying to bond together. We can bond most materials together though, using our very wide range of products and many years of experience. Customers often search using Continue reading
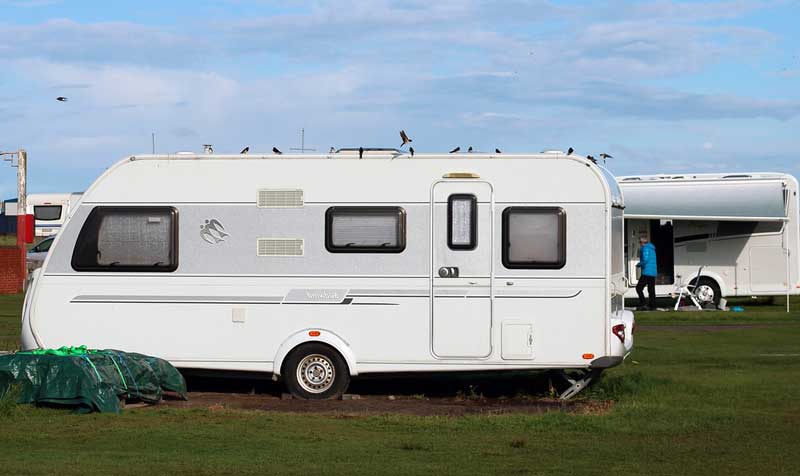
Caravan floor delamination repair
These are caravan floor repair instructions for our CTA 2640 1.1kg kit. If parts of your caravan floor feel spongy or bouncy this can mean de-lamination. The caravan floor is made from polystyrene (also called styrofoam) that is sandwiched between plywood and the base. De-lamination often occurs near the door or in the kitchen area, Continue reading
Crusher Backing resin compound for cone crushers
Crusher Backing resin compound for cone crushers is a 2 part polyurethane system used in cone crushers. It offers superb protection for the mantle and hopper. Our CTA crusher backing resin is used as a shock absorbing compound that prolongs the life of the cone crushing machines. Quarrying and mining industries worldwide use our product Continue reading
Surface preparation for adhesives and best working practice
It is vitally important to ensure the maximum performance of the adhesive or tape is achieved, so we have put together this ‘best working practice’ for adhesive surface preparation. It is always advisable to bond materials together in ambient temperatures i.e. between 15°C and 25°C . The first task before bonding your substrates is surface Continue reading
Metal to metal bonding adhesives
With a wide variety of metal bonding adhesives available, CTA can offer great solutions for your project. We can supply in small amounts or offer bulk purchase solutions for larger businesses. Our experience in the industry is huge and our service is unrivalled. Take a look now at our metal to metal bonding adhesive which is Continue reading
Single part adhesive
CTA have a comprehensive range of single part adhesives and sealants. All one part sealants and adhesives require no mixing and cure with atmospheric moisture or the absence of air depending on the chosen technology. Our 1000 series are highlighted below. Please follow the link to find out more information or purchase the product. Hybrid Continue reading
Two part adhesives
CTA 2000 series consists of our two part adhesives, whereby the resin and activator are automatically mixed prior to application. Two Part Structural Acrylic Adhesive Product Working time Fixture time Type Colour Cartridge size Key Features 2102 4-7 mins 220 mins Hybrid / Methacrylate Neutral 50 / 400ml LSE Plastics Low energy plastic bonder Continue reading
Aerospace adhesives and sealants
Aerospace adhesives and sealants from CTA Industrial Ltd have been developed and tested over many years and can be used for applications such as bonding, filling and repair. We are able to supply military specification products. We are the UK & European distributors for Hernon® able to supply extreme high quality and specification products to Continue reading
Fast Exhibition 2014
Thank you for supporting us at the Fast Exhibition 2014, we hope you enjoyed your time at the Heritage Motor Centre as much as we did, it was nice to meet new people and say hello to some familiar faces. We were overwhelmed with questions about our products and it was great to to spend Continue reading
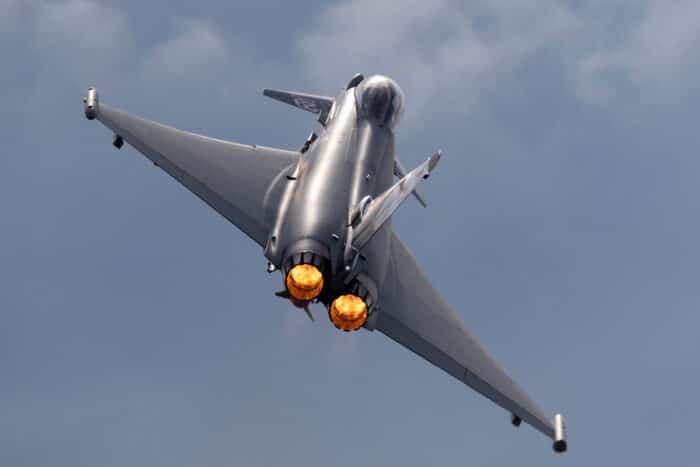
MOD and Aerospace adhesive
MOD and Aerospace adhesives and sealants from CTA Industrial Ltd have been developed and tested over many years and can be used for a variety of applications such as Bullet Sealant, bonding, Thread & Bolt Locking and Bearing Sealants. We are able to supply military specification products. We are the UK & European distributors for Continue reading
Suppliers of tapes and adhesives across the west midlands
CTA have been working closely with local businesses to resolve their bonding issues. They are Suppliers of Tapes & Adhesives across the West Midlands, Birmingham, SuttonColdfield, Erdington, Walsall, Halesowen and surrounding areas. Over the years it has been a main focus to support customers with technical knowledge and backup. Suppliers of tapes and adhesives across Continue reading
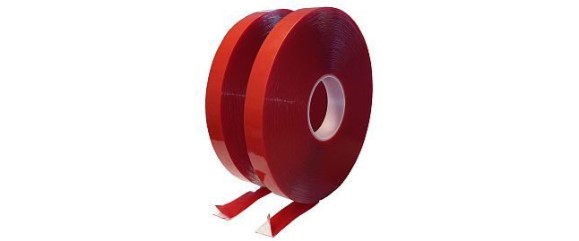
Adhesive Tapes | UK Tapes Supplier
CTA Industrial Ltd are an adhesive tapes supplier in the West Midlands, UK. We provide a wide range of adhesive tape types, including high bond foamed acrylic tapes, high performance tapes, thick double-sided tapes, thin double-sided tapes, single-sided tapes, hook & loop, re-closable fasteners and converted products, such as die cut. Browse our range of adhesive Continue reading
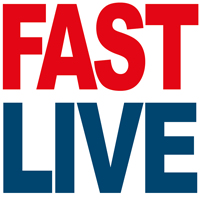
FAST Live Exhibition
CTA were proud to be exhibiting at the “FAST Live” Fastener Exhibition. FAST Live is the UK’s only specialist fastening, bonding and assembly exhibition for engineers, manufacturers and all types of tape, adhesive and fastener buyers. We met lots of great people and enjoyed discussing our new and innovative products. Whatever you’re designing or manufacturing Continue reading
Which Adhesive do I need?
Which Adhesive do I need? A common question when determining which product to bond substrates together successfully. This part of our website including it’s links are an informative guide to assist you in your quest for the right adhesive, giving a basic knowledge and understanding of common terminology used in the industry. • Types of Continue reading
Problem Solving
Problem Solving this category has been designed to share our knowledge on all aspects of bonding to assist you with your projects and understanding of adhesive selection, Joint design, Loads and stresses on bonded joints. At CTA Industrial Ltd, we are always on hand to discuss your application, visit your premises and provide a demonstration Continue reading
Stress loads on adhesive joints
Stress loads on adhesive joints can vary from application depending on the substrates being bonded and how pressure/force is loaded upon a joint. It is difficult to determine how differing stress loads on adhesive joints may affect the overall performance and durability of a bonded joint within an application. Various tests can be performed to ascertain each adhesives optimum performance Continue reading
Adhesive joint design
Adhesive joint design can vary tremendously dependent upon materials, dimensions and various limitations. This section has been put together to help determine and understand the numerous ways of bonding joints together and how this can benefit in strength and performance or adversely be detrimental to the overall performance and durability of the adhesive joint. Their Continue reading
How much adhesive do I need?
How much glue do I need? How much adhesive will I get out of a cartridge? These are the most common questions asked of our technical team here at CTA. Below you will find a quick reference guide to the most popular cartridge and bulk formats used to dispense different adhesives. When Continue reading
Adhesives for transport
Adhesives for transport, CTA’s extensive portfolio of transportation tapes & adhesives are all high specification, quality items, necessary for today’s demanding market. Our high performance products are often used by many OEM’s and meet with the engineers requirements. At CTA we offer a wide range of customised solutions in order to improve manufacturing processes. We Continue reading